Sinonine improves the structure of the autogenous mill, making it more suitable for quartz sand production, and becomes a special equipment for quartz sand with strong adaptability.
At present, in the
silica sand processing plant, the main grinding machines are wheel mills,
rod mills and other processing equipment. Granite is the main material of the roller used in the wheel mill. The stone quality varies greatly due to the different producing areas, which has a certain impact on the processing of quartz sand products. Rod mill is a kind of quartz sand grinding equipment, which uses steel rod as the grinding component and grinds with ore through steel rod. When processing quartz sand products with these two kinds of quartz sand products processing machines, the quartz sand ore feeding particle size is generally less than 50 mm, for large materials, it needs to be grinded by autogenous mill.
Autogenous mill is a kind of media free grinding equipment, which relies on the mutual impact, grinding and grinding of materials. It has the advantages of no medium, large feed size range (up to 600m), no primary crushing of run of mine, convenient use, high output, even discharge, etc. it has been widely used in ore processing industry. However, some special steel materials are used in the components of the traditional autogenous mill, such as manganese steel for lattice plate and lining plate, ductile iron for the lining of discharge dustpan plate and discharge barrel. Therefore, when the wet autogenous mill is used to process quartz sand, these components will frequently collide with quartz sand ore and cause wear, and the iron scraps produced will be mixed with it. Among the quartz sand products, it will also cause pollution to the quartz sand products, and most of the iron scraps produced can not be removed by subsequent
magnetic separators, which greatly increases the iron content in the quartz sand products and seriously affects the quality of the quartz sand products. In addition, the traditional autogenous mill is used to screen the quartz sand ore on the lattice plate. The discharge hole on the lattice plate is a strip discharge hole. There are some larger quartz sand particles in the quartz sand screened through the strip discharge hole. Therefore, the autogenous mill is equipped with a large cylinder made of carbon steel material, which is used to screen the larger quartz sand through the cylinder self return screen The particles return to the grinding cylinder for grinding again, which not only complicates the structure of the autogenous mill self, but also causes frequent impact and wear between the quartz sand particles and the cylinder self returning screen, producing iron chips and entering the quartz sand products, which affects the quality of the quartz sand products. At the same time, due to the large size of the self returning screen, this not only complicates the structure of the autogenous mill, makes it difficult to maintain the equipment and transport it , and the rotation rate is low and the weight is large, which increases the working strength of the driving device of the autogenous mill.
In view of the above technical problems, Sinonine technical team has improved the structure of the traditional autogenous mill to make it more suitable for quartz sand production and become a special equipment for quartz sand with strong adaptability. It can greatly reduce the production of iron filings in the processing of quartz sand products, improve the quality of quartz sand products, reduce the production cost, and the structure is simple.
The technical scheme of the technical improvement is as follows:
The autogenous mill for quartz sand processing includes the cylinder, the cylinder is connected with a discharge cylinder, the inner cavity of the cylinder is provided with a grid plate, on the grid plate are a number of discharge holes for screening the materials after autogenous grinding, the cylinder is also provided with a dustpan plate for conveying the screened materials to the discharge cylinder; the autogenous mill also includes a feeding device for conveying ore materials to the cylinder and a driving device for driving the operation of the autogenous mill. The grid plate includes a mesh support body, and the surface of the support body is covered with an elastic wear-resistant layer; the discharge hole of the autogenous mill is a conical hole, and the feeding end of the discharge hole is smaller than the discharging end. The dustpan plate of the autogenous mill includes a dustpan like shell, and the inner surface of the shell is provided with an elastic wear-resistant layer. A rubber lining plate is arranged on the inner surface of the cylinder to increase the wear resistance.
For the autogenous will with the above structure, since the lattice plate with elastic wear-resistant layer is used, the discharge hole of the lattice plate adopts the conical hole with the feeding end smaller than the discharging end. This structure, through the impact of the elastic wear-resistant layer and the quartz sand particles, avoids the production of iron chips, reduces the iron content in the quartz sand products, improves the quality of the quartz sand products, and avoids the bullet. Because of the elasticity of the wear-resistant layer, the quartz sand particles are blocked when they are discharged through the discharge port, which can make the quartz sand particles screened through the discharge hole smaller, so as to remove the self return screen, avoid the pollution of the quartz sand and the iron chips produced by the abrasion of the quartz sand and the self return screen to the quartz sand products, further improve the quality of the quartz sand products, and simplify the process The structure of autogenous mill reduces the production cost. In the same way, the composite dustpan plate and discharge cylinder composed of shell and elastic wear-resistant layer are used to avoid the generation of worn iron scraps of autogenous mill parts, greatly reducing the iron content of quartz sand products, so that the iron content of quartz sand products can be reduced from 0.08% to 0.02%, improving the quality of products. The rubber elastic wear-resistant layer and carbon steel dustpan shell, discharge cylinder shell and lattice plate support body not only ensure the strength and service life of the parts, reduce the production cost of the parts, but also greatly reduce the weight of the parts , thus reducing the working strength of the drive device and saving energy consumption.
The structure of traditional autogenous mill is shown in the figure below:
The traditional autogenous mill is equipped with a self returning screen 7. Driven by the driving device 4, the autogenous mill operates. The quartz sand ore transported from the feeding device 2 is self grinded by the cylinder 1, and then the quartz sand particles are screened by the grid plate with strip discharge holes. The screened quartz sand particles are transported from the discharging dustpan to the self returning screen 7 at the discharge cylinder, and the particles are compared by the self returning screen 7 Large quartz sand particles return to cylinder 1 for self grinding, while smaller ones are transported to the next process. When quartz sand ore is processed in the autogenous mill, quartz sand ore and particles will collide and wear with the inner lining, grid plate, dustpan plate, discharge cylinder and self return screen of the grinding cylinder frequently, and a large number of iron scraps will be mixed into quartz sand products, causing pollution to quartz sand products, while the inner lining, grid plate, dustpan plate, discharge cylinder and self return screen of the grinding cylinder are all made of special steel materials, so the iron chips produced by them are difficult to be removed by the magnetic separator in the later process, which seriously affects the quality of quartz sand products. At the same time, due to the large size of the self return screen, it not only makes the structure of the autogenous mill complex, which makes the equipment maintenance difficult and the operation rate low, but also the weight of the self return screen, the grinding cylinder, the grid plate, the dustpan plate and the discharge cylinder are relatively heavy, which makes the working strength and the working load of the driving device 4 higher.
The improved autogenous mill includes a cylinder 1, a feeding device 2 which can transport materials for cylinder 1 and a driving device 4 which can drive the autogenous mill to operate, a discharging barrel 3 which is connected with cylinder 1, a lattice plate 5 which is arranged in the inner cavity of cylinder 1, and a dustpan 6 which can transport the screened materials to discharging barrel 3.
As shown in the figure below, the lattice plate 5 is provided with a number of discharge holes 51 that can screen the ground material, and a mesh support 52. The surface of the support 52 is covered with an elastic wear-resistant layer 8. Through such a design, a composite lattice plate is made.
In this way, when the quartz sand ore is self grinded in the cylinder 1, the elastic wear-resistant layer 8 is used to collide with the quartz sand ore for wear, so as to avoid the generation of iron chips, reduce the iron content in the quartz sand product and improve the quality of the quartz sand product; because the lattice plate 5 needs to maintain high strength and long service life in the work, the support body 52 can be mined carbon steel plate support with mesh is made of carbon steel material, such as 12mm thick carbon steel plate support, which not only ensures the strength of the lattice plate, but also lightens the weight of the lattice plate, while the elastic wear-resistant layer 8 can be made of rubber elastic wear-resistant layer, which can be made of rubber steel composite lattice plate through rubber vulcanization and lattice plate; while the discharge hole 51 can be designed into the shape of a conical hole, such as a bevel. The feeding end of the discharging hole 51 is smaller than the discharging end, that is, the end of the discharging hole 51 close to the quartz sand ore in the self grinding state in the barrel 1 is smaller than the end of the discharging quartz sand particle from the dustpan plate 6. In this way, the quartz sand particle will not cause blocking when it is discharged through the discharging hole 51, so that the quartz sand particle can pass through smoothly, and the discharging end is smaller than the discharging end. The quartz sand particles screened through the discharge hole become smaller, so as to remove the self returning screen, avoid the pollution of quartz sand products caused by quartz sand particles and iron scraps from the abrasion of the self returning screen, simplify the structure of autogenous mill, reduce the weight of autogenous mill, and reduce the working intensity of the driving device of the autogenous mill.
The following figure is the structure diagram of dustpan plate 6
The dustpan plate 6 is also designed as a composite dustpan plate. The dustpan shell 61 in dustpan shape can be used. The inner surface of the dustpan shell 61 which is in contact with the quartz sand particles is also provided with an elastic wear-resistant layer 8. Thus, when the quartz sand particles screened by the grid plate are transported from the discharge dustpan plate to the discharge cylinder, the quartz sand particles only contact with the elastic wear-resistant layer 8 and wear, which also avoids the generation of iron chips In order to reduce the iron content in quartz sand products and improve the quality of quartz sand products, the dustpan plate 6 should be squeezed with the lattice plate and frequently worn with quartz sand particles in the work, so it also needs to maintain a certain strength and long service life. Therefore, the dustpan shell 61 can also be made of carbon steel, such as 8m thick carbon steel plate On the premise of ensuring the working strength of the dustpan, the weight of the dustpan is reduced. The rubber elastic wear-resistant layer 8 is also used. The rubber steel composite dustpan 6 can be made by bonding and fixing between the rubber elastic wear-resistant layer and the carbon steel dustpan shell.
The following figure is the structural diagram of discharge cylinder 3.
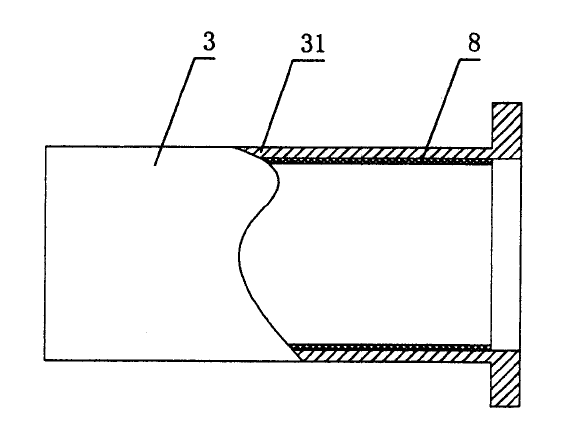
The discharge cylinder 3 is used to transport the quartz sand processed by self grinding to the next process parts, and there is contact wear with the quartz sand particles. Therefore, the discharge cylinder 3 also adopts the composite design, which designs the discharge cylinder 3 into a composite liner type discharge cylinder. Through a discharge cylinder shell 31, the inner surface of the discharge cylinder shell 31 is provided with an elastic wear-resistant layer 8, just like the grid plate and dustpan plate, the discharge cylinder shell 31 is provided with an elastic wear-resistant layer 8. Cylinder 3 also needs to maintain a certain strength and long service life in the work. Therefore, the discharge cylinder 3 is also made of carbon steel, and the discharge cylinder shell 31 is made of 8mm thick carbon steel plate, which not only ensures the strength of the discharge barrel, but also reduces the weight of the discharge cylinder. The elastic wear-resistant layer 8 also uses the rubber elastic wear-resistant layer, the rubber elastic wear-resistant layer and the carbon steel discharge barrel cylinder 31 .The rubber steel composite discharge barrel is made by bonding and fixing.
Because the inner of cylinder 1 is the place where the autogenous mill and quartz sand ore collide and wear the most frequently and seriously during operation, the inner of cylinder 1 can be equipped with rubber lining plate 11 to separate quartz sand ore from cylinder 1 through rubber lining plate 11, so that when the autogenous mill works, quartz sand ore and rubber lining plate 11 contact and collide to avoid producing iron chips to quartz sand products pollution.