This article shares an efficient dry method sand making technology and
sand making machine adopted.
VSI sand making machine is widely used in wet sand production. This process has the advantages of good sand quality and high production efficiency, but it requires a lot of water, which brings a lot of problems in the treatment of sediment-containing wastewater and serious environmental pollution. In the wet sand production process, because of the use of water, the production efficiency is also reduced, the field calculation efficiency can be reduced by more than 40%, and because of the existence of water, the equipment is easy to rust, which leads to worsening and shorten the service life of sand making machine parts. In the follow-up process of wet sand preparation, a large amount of water is used to clean and remove dust, which not only causes the loss of small size particles (about 10%), but also causes a large number of waste disposal problems after washing
by sand washing machine.
Sinonine technical team has studied the dry sand making process and formed a complete
sand making system and s
and making equipment. Dry sand making focus on dealing with serious dust problems, and solve the problems from both the sand making machine itself and the whole system. A dry sand making machine with crushing and cleaning functions is provided, which has high production efficiency and low environmental pollution.
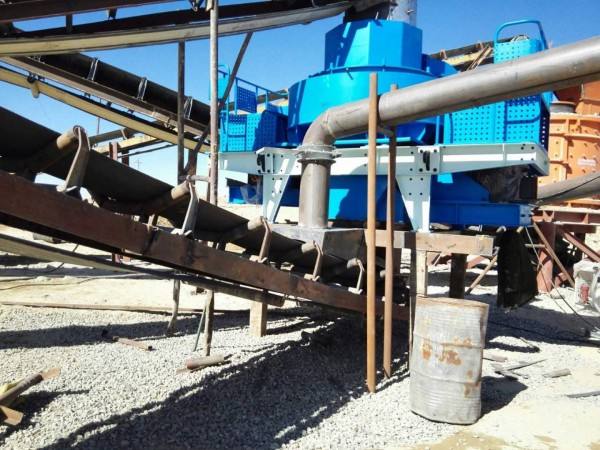
The new
sand making machine includes a hollow crushing working chamber. The upper surface of the crushing chamber is provided with a feed port, and the lower surface is provided with a lower feed port. A rotor and a crushing device are arranged in the crushing working chamber. A hollow dust removal working chamber is arranged below the crushing working chamber, the upper end of the blanking passage is connected with the sealing of the blanking passage, the lower end of the blanking passage is located in the inner part of the dust removal working chamber, and an air outlet connected with the inner part of the dust removal working chamber is arranged on the dust removal working chamber. The air passage with both upper and lower openings is located in the inner part of the dust removal working chamber, and the material removal is communicate The lower end of the duct and the upper end of the duct are staggered horizontally. The bottom surface of the dust removal working chamber is provided with an outlet. After passing through the outlet, the dust collection assembly is connected with the lower end seal of the air duct, or the dust collection assembly is connected with the air outlet seal.
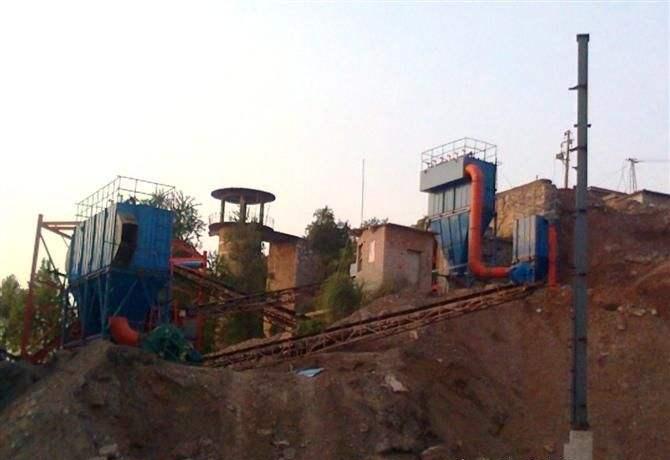
This sand making machine will set the dust removal chamber below the crushing chamber to make full use of the favorable distribution of crushed materials for dust separation. Because the material is relatively dry after high-speed impact and friction heating, and the dust has not yet touched the surface of the material, so the dust is easy to be separated and removed, so a good dust removal effect can be obtained. In addition, after the material is crushed in the crushing working chamber, the material gradually separates from each other, there is no blocking phenomenon in the dust removal link, and there is little chance of dust being contaminated on the material particles, so the dust removal efficiency is high and the effect is better. At the same time, the strong airflow formed by the impact crushing of the sand making machine rotor can mix and drive the dust removal airflow, thus reducing the power demand of the dust removal fan and energy consumption.
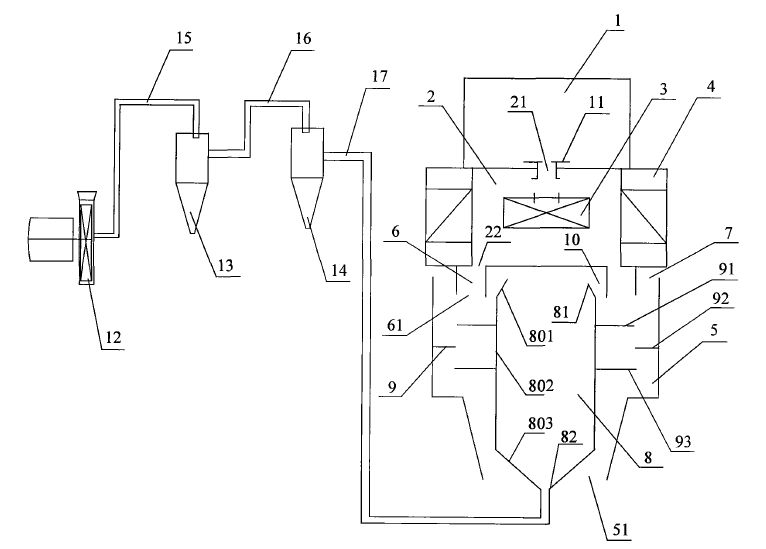
The working process of the sand making machine is as follows:
The raw material in the feeding hopper 1 enters the working chamber 2 of the crusher through the feeding port 21. The rotor 3 drives the material to throw to the crushing device 4 at high speed driven by the motor. After the violent collision between the material and the crushing device 4, the material is crushed into small particles.
Material moulding composed of crushed stone and dust is passed through the discharge passage 6 by the discharge outlet 22 and then enters the dust removal chamber 5. Because the discharge passage 6 is sealed with the discharge outlet 22, it can ensure that all the materials are entered into the dust removal chamber 5, thus preventing dust spillover. Material moulding will be blocked by windshield 91, 92, 93 in turn, then continue to fall, so as to form an upward airflow zone, which can separate the particles from the sediment and prevent the particles from being misinhaled into the dust collecting assembly. Because of the function of the dust collecting assembly, the interior of the crushing working chamber 2 and the dust collecting working chamber 5 are in a negative pressure state. At this time, the outside wind can enter the dust removal chamber 5 from three entrances. The three entrances are: 1) the inlet and outlet 21, 2) the vent 7, and 3) the outlet 51 at the bottom of the working chamber 5.
The material cleaned by airflow continues to descend under the action of gravity, and the air entering from outlet 51 moves from bottom to top, with the residual dust in animal material moving upward together. After passing through the pipeline settlement area 10, it enters the airway 8 and eventually discharges from the suction fan 12.
The clean material after dust removal is eventually discharged from the sand making machine at the outlet 51 at the bottom of the dust removal chamber 5.
Under the action of the induced draft fan 12, the dust passes through the pipeline 17 before entering the dust collector 14 for the first time cleaning, and the air after the dust removal passes through the pipeline 16 into the dust collector 13 for the second time cleaning. After such two dust removals, the clean air can meet the requirements of environmental protection. After 15 pipelines, the air is eventually discharged from induced draft fan 12.
Suggestions: Dry method sand making can save cost and reduce energy consumption. At the same time, you also need to ensure that the humidity of raw materials is appropriate, if the raw materials contain a certain amount of water, it will affect the production effect.