In the field of
silica sand processing and
sand washing plant, in order to obtain high-grade quartz sand or to treat low-grade refractory quartz sand, flotation method is needed. A successful application of treating pyrite-type quartz sand by flotation method is introduced in detail in this paper.
Pyrite-type quartz sand ore
Quartz sandstone is a consolidated clastic rock. Its quartz clastic content is more than 95%. It comes from various magmatic rocks, sedimentary rocks and metamorphic rocks. The associated minerals are feldspar, mica and clay minerals, and the cements are mainly siliceous cements. Quartz sandstone is the main source of siliceous mineral materials for glass, ceramics, foundry and other industrial quartz sands. Because quartz sandstone contains impurities such as associated minerals and cements, it must be purified by beneficiation before it can be used in industry.
Pyrite-type quartz sandstone deposits have huge ore reserves, which have not been exploited and utilized for lack of effective purification technology. Sinonine has carried out technological mineralogical research on this kind of quartz sand ore. The results show that it is a siliceous argillaceous medium-grained feldspar-bearing quartz sandstone. The original ore is mainly quartz with a particle size ranging from 0.2 to 0.5 mm (32 meshes to 80 meshes). At the same time, it contains a small amount or trace of other impurity minerals, such as pyrite, montmorillonite, illite, kaolinite, microcline and square. Calcite and other minerals have a great influence on ore quality, such as pyrite and clay minerals, in which pyrite content is less than 1% (particle size is 0.02-0.10 mm), clay mineral content is about 8%, they are disorderly dispersed among quartz particles with interstitial fillings; raw ore SiO 2 content is 94.02wt%, while harmful components such as A12O3 (3.88wt%) and K2O (1.28wt%) occur in montmorillonite and iranite. Fe2O3 (0.09wt%) mainly comes from pyrite and partly from clay minerals.
In order to further clarify the influence of pyrite on the quality of quartz sand ore, various methods were used to test and analyze. The following is a polarizing microscope photograph of the original pyrite-type quartz sandstone deposit. It can be seen from the graph that the pyrite in the ore is a black opaque irregular granular mineral with a particle size distribution of 0.02-0.1 mm. It is disorderly distributed and interpenetrated between quartz grains or enclosed in impurities. The boundary is not clear. Obvious weathering phenomenon has taken place. Some clay minerals are filled in the voids produced by the weathering of pyrite.
The following figure is the result of X-ray powder diffraction (XR) analysis of fine pyrite grains, which proves that pyrite grains contain clay minerals such as kiangling clay. The results of chemical composition analysis (XRF) showed that the proportion of fine Fe2O3 and SO3 in pyrite was 8.50wt% and 8.05wt % respectively. Meanwhile, the content of Al2O3 was 23.58wt%, and the contents of CaO (5.10wt%) and MgO (1.19wt%) were also higher. Therefore, the pyrite particles in the ore are actually a mixture of weathered pyrite and clay minerals. Pyrite particles are not only the main carrier of harmful impurity Fe2O3, but also the carrier of some harmful components such as Al2O3 and CaO. In a word, pyrite exists in quartz sandstone ores as fine grains and becomes the carrier of harmful components such as Fe2O3, Al2O3 and CaO.
Index requirement of float glass quartz sand
The technical indicators of quartz sand for float glass are usually: SiO2 (+98.6%) (permissible fluctuation range 0.3%), A12O3 <0.2%, Fe2O3 <0.09%, titanium dioxide <0.08% and 30-150 meshes (>94.5%). Therefore, the main harmful mineral pyrite must be removed by proper purification process when quartz sandstone ore with the above characteristics is used to process quartz sand for glass industry.
Pyrite ore and its beneficiation
Pyrite, chemical composition FeS, its crystal belongs to equiaxed sulfide minerals. The theoretical composition of pyrite (wt%): Fe46.55, S53.45. The isomorphism of Co and Ni often replaces Fe to form FeS2-CoS2 and FeS2-NiS2 series. Common crystals are cubes, pentagonal dodecahedrons, octahedrons and their aggregates. There are stripes parallel to the crystal edges on the cubic crystal plane, and the stripes on each crystal plane are perpendicular to each other. The color of pyrite is light yellow or brass, with green or brown-black streaks, strong metallic luster, opacity, non-cleavage and uneven fracture. Hardness 6-6.5, specific gravity 4.95-5.20, melting point 1171 degree, brittle. Limonite is easily weathered under surface conditions. Pyrite is a semiconductor mineral with weak conductivity and thermoelectric properties. It is insoluble in water and dilute hydrochloric acid, soluble in nitric acid and has sulfur yellow precipitation.
Pyrite is one of the most widely produced sulfide minerals in nature and widely used. However, pyrite sometimes exists as an associated impurity of non-metallic minerals, which will have an impact on mineral properties. When Fe and S exist in the form of trace elements, they are harmful and will affect the quality of products. It is very important to extract pyrite as a harmful component.
Removal of pyrite is a very important work in the processing of non-metallic minerals. According to the chemical properties of pyrite, acid-base method is not suitable. According to its physical properties, pyrite has weak or almost no magnetism and can not be effectively removed by magnetic separation. In addition, there are also gravity and flotation methods to choose from. The proportion of pyrite is 4.95-5.20, which is larger than that of non-metallic minerals.
In theory, it can be removed by gravity selection. However, pyrite particles in pyrite-type quartz sandstone are small and cemented with clay and other minerals, which is not conducive to gravity separation and removal. Pyrite can be floated from non-metallic mineral raw materials by using ethyl xanthate, butyl xanthate and other reagents as collectors of pyrite and 2 # oil as foaming agents.
Laboratory test of silica sand flotation to remove pyrite
According to the above description, Sinonine has carried out flotation test on pyrite-type quartz sand and achieved very good results. The first step is to compare flotation schemes under different reagent systems with raw sand-20 mesh 100% as test samples; the second step is to adopt flotation schemes with better effect and take raw sand-20 mesh 100% as test samples to carry out flotation pH, pulp concentration, reagent dosage, flotation time and other technological parameters tests; the third step is to adopt optimum flotation process. The comprehensive effect verification test was carried out with 40-150 mesh quartz sand as test sample. All samples were analyzed by
Shimadzu XRF-1800 X-ray fluorescence spectrometer (XRF). The test method was powder tablet method.
In view of the characteristics of less pyrite, according to the principle of "suppressing more and less flotation", we adopt single cell flotation machine and reverse flotation process to remove iron, that is, the flotation method of pyrite and its inclusion bodies and collectors into the flotation froth layer, and the quartz sand concentrate to remain at the bottom of the flotation cell. The operation procedures are as follows:
PH of silica sand slurry on iron removal effect
Under the conditions of 25% pulp density, 200 g/t of combined collector (ethyl xanthate: butyl xanthate = 4:1), 15 min of flotation time and 75 g/t of foaming agent 2 # oil, the effect of collector on iron removal by flotation under different pH values was investigated. The results of the experiment are as follows.
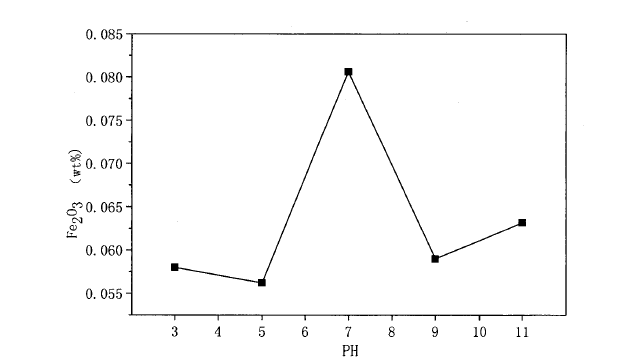
The change of
silica sand pulp pH has great influence on the flotation effect. When pH=5 and pH=9, the iron removal effect is better, and when pH=5, the iron removal effect is the best, which indicates that weak acidic environment is the most favorable for the flotation of pyrite by the combined collector.
Slurry density on iron removal effect
The effect of different pulp density on iron removal was investigated under the conditions of pulp pH 5, combined collector (ethyl xanthate: butyl xanthate = 4:1) dosage of 200 g/t, flotation time of 15 min and foaming agent dosage of 75 g/t. The experimental results are shown in the following figure.
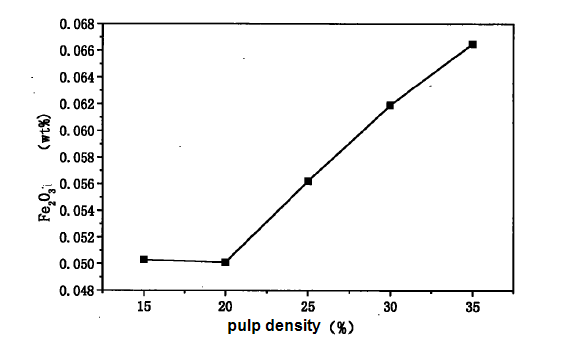
As can be seen from the above figure, the effect of pulp density on iron removal by flotation is very obvious. Among them, the effect of iron removal by flotation is better at 15-20% low pulp density. When pulp density exceeds 20%, with the increase of pulp density, the iron content in concentrate increases gradually, and the effect of iron removal by flotation becomes worse and worse. Therefore, 20% pulp density is suitable
Collector dosage on iron removal effect
The effect of combined collector (ethyl xanthate: butyl xanthate 4:1) on iron removal was investigated under the conditions of pulp pH=5, pulp density 20%, flotation time 15 min and foaming agent 2 # oil dosage 75 g/t. The results are as follows.
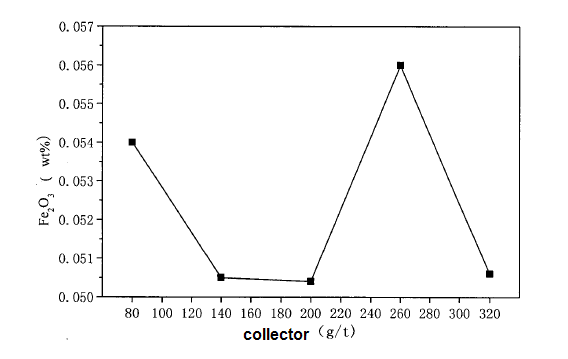
From the above figure, we can see that the content of Fe2O3 does not decrease with the increase of collector dosage. When the dosage of collector is 200 g/t, the content of Fe2O3 is the lowest. This may be because excessive collector will fail in hydrolysis reaction in acidic medium, thus losing the ability to collect pyrite, so the dosage of collector should be around 200 g/t.
Flotation time on iron removal effect
Under the conditions of pH=5, 200 g/t of combined collector (ethyl xanthate: butyl xanthate 4:1), 20% pulp concentration and 75 g/t of foaming agent 2 # oil, the effect of different flotation time on iron removal was investigated. The experimental results are as follows.
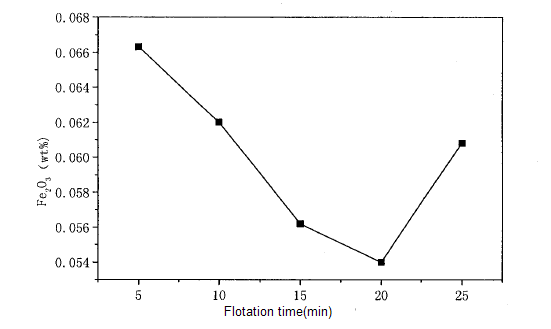
The results show that the flotation time is between 5 and 20 minutes, and the basic trend is that the content of Fe2O3 decreases gradually with the prolongation of flotation time, with the largest decrease in the first 5 minutes and the slower decrease in the content of Fe2O3 after 15 minutes. When the flotation time exceeds 20 minutes, the content of Fe2O3 increases. It may be that with the prolongation of agitation time, xanthate is oxidized gradually by free oxygen in the pulp and loses the function of collecting pyrite. The collected pyrite returns to quartz sand, which leads to the increase of the content of Fe2O3 in the concentrate. Therefore, from the point of view of saving cost and time, the suitable flotation time is 15 minutes.
In summary, better purification effect can be obtained by using combined collector (ethyl xanthate: butyl xanthate = 4:1) in reverse flotation. The optimum flotation parameters are as follows: pulp pH = 5, pulp concentration 20%, combined collector (ethyl xanthate: butyl xanthate = 4:1) dosage 200 g/t, flotation time 15 min, foaming agent 2# oil 75g/t.
Silica sand flotation processing of Iron removal
After the above flotation treatment, the chemical composition and particle size of the concentrate of quartz sand can meet the technical requirements of quartz sand for floatation glass. Thus, an iron removal process suitable for processing quartz sand for glass industry with pyrite-type quartz sandstone as raw material can be obtained, i.e. using quartz sand
flotation machine, combined collector and reverse flotation iron removal and purification process, and processing quartz sand for glass industry can achieve obvious comprehensive purification effect. The specific process is as follows.
The process steps are as follows
A.Crushing and screening: crusher,
rod mill and vibrating screen are used to process raw materials into - 40 mesh materials.
B. Washing& desliming: The silica sand material of 40-150 mesh was classified by the
hindered settling classifier and
hydraulic classifier. At the same time, the quartz sand was washed and desliming by
attrition scrubber,
spiral sand washing machine and desliming cone.
C.Magnetic separation iron removal: wet
drum magnetic separator is used to remove mechanical iron in quartz sand.
D. Adjust the pulp density: weigh the required weight of silica sand material and add it to the
conditioning tank, then adjust the pulp density to 20% with fresh water;
E. Adjust the pulp pH value: 20% sulfuric acid was used to adjust the pulp pH value to 5, and then the pulp conditioning tank was used to mix for 2 minutes.
F. Adding collector: Ethyl xanthate: butyl xanthate = 4:1 combined collector was added to the pulp according to the dosage of 200 g/t, and then agitated for 3 minutes by
flotation machine.
G..Adding foaming agent: adding foaming agent 2 # oil into pulp according to the dosage of 75g/t, then mixing for 2 minutes with flotation machine;
H.Scraping bubbles: Open the inflatable valve of flotation machine and scrape bubbles for 15 minutes.
I. Material cleaning: After the Scraping stop, the quartz sand material in the flotation machine tank bottom is cleaned by fresh water, that is to say, the quartz sand concentrate is obtained.
Conclusion
The flotation process can effectively treat pyrite-type quartz placer. The process has advantages of obvious purification effect, simple process, low cost, easy popularization and application, and wide application etc. It can be used as the main production process of silica sand purification.