In
silica sand processing plant and
sand washing plant, the VSI
sand making machine is a core equipement. As the executive part of VSI sand making machine, the service life of the rotor directly determines the maintenance cycle and startup rate of the equipment. Although the rotor will inevitably be worn in production, the correct analysis of its wear, the establishment of replacement standards and maintenance methods will greatly improve the operation of the whole equipment and extend the actual service life.
Structure of rotor of VSI sand making machine
The rotor of VSI sand making machine is mainly composed of rotor body, distributing cone, feed ing hole and pipe, guide plate, upper wear plate, lower wear plate and top wear plate. In the process of daily maintenance, it mainly includes the regular replacement of worn parts and the welding repair of rotor body wear. The equipment maintenance and operation personnel can determine the operation status of the whole equipment through the wear condition of each part of the rotor.
Wear analysis and maintenance method of polishing head
The wear part of the polishing surface presents a central symmetrical arc-shaped wear depression. When the residual amount of wear-resistant insert is less than 3mm, it shall be replaced in time.
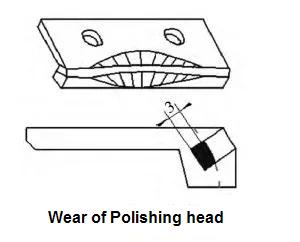
The polishing surface shows a middle arc-shaped wear depression, and the wear part is up or down. When the residual amount of wear-resistant insert is less than 3mm, it shall be replaced in time. At the same time, it is necessary to adjust the angle of the guide plate and the thickness of the accumulated material in the crushing chamber to completely solve the side wear.
Replace the cracked or cracked polishing head in time, check whether there is iron inclusion in the feeding, whether the feeding force is too large or whether there is sand inclusion on the assembly surface, adjust and clean up in time to avoid similar situations.
Wear analysis and maintenance method of upper and lower wear plates
From the inner surface of the wear plate to the discharge opening, there is gully wear. When the thickness allowance of the wear plate at the maximum wear position is less than 3mm, it is necessary to replace it.
When the feed barrel and feed hole sleeve are seriously worn, it is necessary to check the wear of the feed barrel and feed hole sleeve and replace them (when the inner edge of the upper wear plate is worn to 3mm), observe the wear position of the rotor throwing head, and determine whether it is affected by the installation position and angle of the guide plate.
It is necessary to check the wear condition of the distributing cone. The wear of the distributing cone will directly aggravate the wear rate of the lower wear plate (the thickness allowance at the maximum wear position of the distributing cone is less than 3mm or the fixed bolt top must be replaced when it starts to wear). At the same time, observe the wear position of the rotor throwing head to determine whether it is affected by the installation position and angle of the guide plate.
Wear analysis and repair standard of rotor main body
The wear of rotor main body is mainly reflected in three aspects: top edge wear, bottom edge wear and inner side wear. It needs to be repaired manually and periodically, following the principle of "small repair and frequency repair".
The wear of the top edge of the rotor must be accompanied by the excessive wear of the top wear plate. The top wear plate shall be replaced before it is worn to the rotor body.
Generally, the reason of rotor bottom edge wear is that the deposit angle at the bottom of the rotor rubs the bottom and the edge of the rotor, so the deposit at the bottom of the rotor should be reduced reasonably.
The wear on the inner side of the rotor usually occurs when the feed is fine or the material flow is large. The streamline wear of the gap or edge between the material and the installation position of the wear plate and the rotor body needs to be filled with urethane sealant after the installation of the wear plate or the polishing head.
The repair of the worn part of the rotor is mainly divided into two parts: the repair of the worn part and the surface hardening repair of the worn part. The welding repair operation is not allowed in the general assembly of the equipment and on the balancing machine.
When the wear part is used for repair, the electrode of the same material as the rotor body shall be used, and the repair shall be carried out according to the original size of the rotor.
When the surface hardening repair is adopted, the hardening repair of the top edge wear only needs to be carried out on the basis of the repair of the wear part, with the thickness ≥ 5mm, the thickness of the lower surface hardening layer ≥ 2mm, and the radial hardening repair length ≥ 20mm. If the bottom edge is worn, the upper and lower surfaces and side edges of the rotor bottom shall be welded and hardened. After repair, the dynamic balance of rotor shall be kept unchanged.
When the thickness allowance of the worn parts of the rotor is less than 3mm, it is necessary to shut down the machine for complete replacement within 8h of the equipment operation, and find out the cause of wear. The repair of rotor body shall strictly comply with the repair standards to ensure that the repair quality and dynamic balance meet the production requirements.
During the use of the rotor of sand making machine, it is necessary to periodically check manually and measure the allowance after wear, and replace the worn parts and weld the rotor body in strict accordance with the replacement and maintenance standards.