The
dewatering screen uses the vibration motor as the excitation source, so as to obtain high-frequency vibration, and to produce high-efficiency dewatering effect. The volume of the dewatering screen is small, the noise is low, and it will not cause any pollution to the environment. In the
sand washing plant, in order to better improve the dewatering effect of the dewatering screen, SINONINE tech team suggests that the following factors should be fully considered.
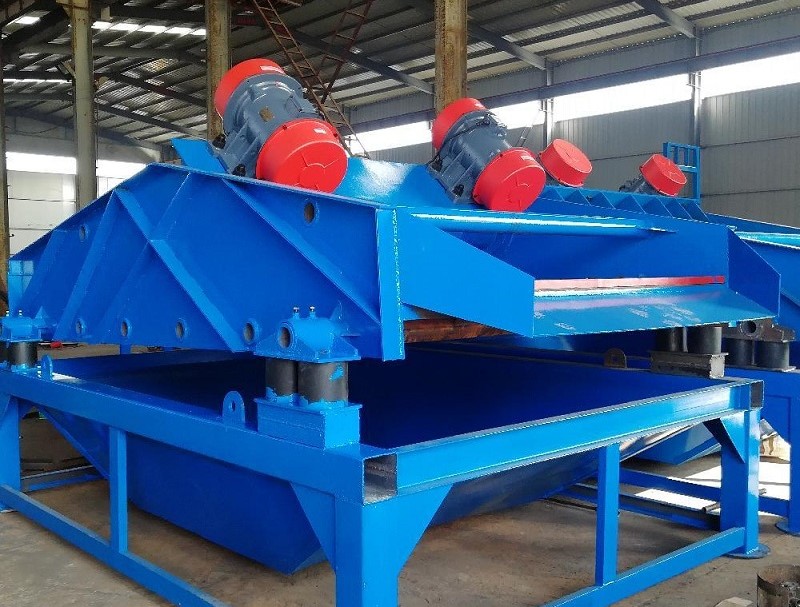
1.The influence of material particle shape on dewatering effect of dewatering screen.
There are many shapes of material particles to be dehydrated, such as spherical, cubic, polygonal, flat row, flaky and so on. According to SINONINE's experience for many years, there are enough voids between spherical, cubic and polygonal material particles, which can be easily dehydrated. The dewatering efficiency will be more than 50% higher than that of flat and flaky material particles. The settlement resistance of flat and flaky material particles is large, which is not conducive to dehydration. Therefore, when users choose the capacity of dewatering screen, they should fully consider the influence of material shape on dewatering effect.
2.The effect of particle size and its characteristics on the dewatering effect of the dewatering screen.
The particle size distribution of the material also has a great influence on the dewatering effect of the dewatering screen, and the proportion of the fine material has a great influence on the dewatering effect. The screen mesh size should be matched according to the average particle size of the material to keep a certain proportion of particles larger than the average particle size, so as to improve the dehydration effect.
3. The influence of material density on dewatering effect of dewatering screen.
If the density difference between solid and liquid is small, the possibility of solid particles losing with liquid will increase in the dewatering process. At this time, the flow rate of materials should be slowed down, the residence time of materials on the screen should be prolonged, and the inclination angle of the dewatering screen should be increased.
4. The influence of material composition on dewatering effect of dewatering screen
If the content of clay material is large, the slurry viscosity will increase, which is not conducive to dewatering. A single material has a single material layer structure than a variety of composite materials, and the dewatering effect is better and faster than a variety of composite materials.
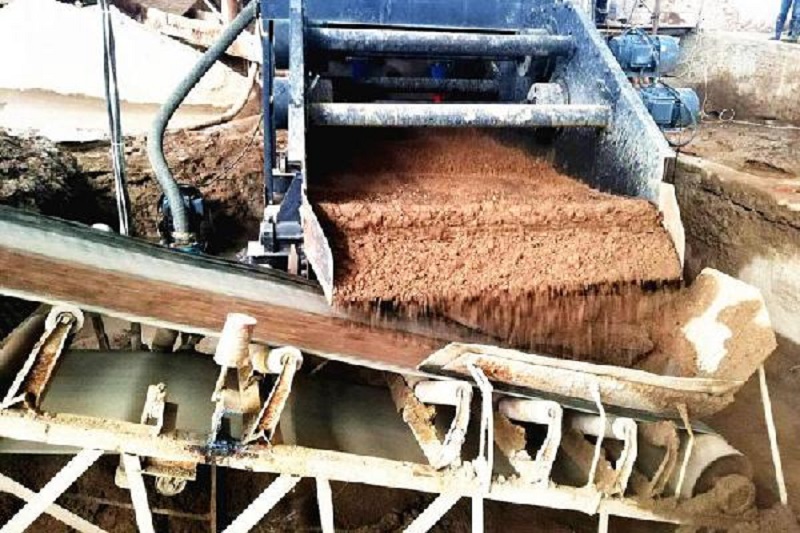
In addition to fully understanding the influences of the above on the dewatering effect of the dewatering screen, customers should match the dewatering screen with appropriate parameters according to the properties of the dewatered materials, and then fully consider the following technical conditions when using the dewatering screen, so as to ensure that the dewatering screen operates in the best working condition and improve the dewatering effect.
1.The working environment of the dewatering screen shall be free of conductive dust, inflammable, explosive and corrosive gas.
2. the working altitude of the dewatering screen shall not exceed 1000m. If it is more than 1000m but not more than 4000 meters, the temperature rise limit shall be reduced by 0.5 ℃ for every 100 meters increase.
3. The vibration acceleration of the dewatering screen shall not exceed 19.6m/s, that is, 20 times of the gravity acceleration.
4. The ambient temperature of the dewatering screen shall not exceed 40 ℃, and if it is more than 40 ℃, the power shall be reduced.
5. The working power supply of the dewatering screen is generally three-phase 380V with a frequency of 50Hz. If the power supply changes, the working parameters of the dewatering screen should be adjusted.
6.The working mode of the dewatering screen is continuous work, so as to ensure its continuous operation and the machine can not be opened and stopped frequently.
7.The stator winding temperature of the vibrating motor of the dewatering screen rises by less than 80K.
8. The allowable temperature rise of the bearing of the dewatering screen shall not exceed 95 ℃.
9. The working current of the dewatering screen shall not exceed the data on the motor nameplate, otherwise, the use of excitation force shall be reduced accordingly.
For more information about dewatering screen and sand washer, please visit SINONINE website www.9silica.com , or contact us directly + 86-18118821087 (WhatsApp).